Anodizing Defects Pdf
- You zero in on the cause of defects: • Try replating the part using the same procedures and equipment. To assist with your troubleshooting, this section.
- Typically for Conventional and CLASSIC Hard Coat. The hard coat anodizing process has secondary factors such as chemical polishing steps. What are Edge Defects?
Defect Analysis of the Aluminum Alloy Substrate after Chromic Acid Anodizing- -《Surface Technology》2. YANG Jing- wei; ZHAO Yong- gang; SUN Jie; HU Sheng- nan.
. 474 Downloads. Abstract Streaking is a common surface defect on anodized extrusions of 6xxx series soft alloys. Very often, the defects only become apparent after anodizing, which makes it difficult to identify their root cause. In industry practice, a trial-and-error method has been taken to reduce the intensities of the streak defects, greatly increasing the fabrication cost. This paper describes the formation mechanism of various streak defects on the basis of a literature review and experimental results. This provides a basis for developing effective measures for preventing the formation of these defects for the extrusion industry.
Keep your software up- to- date. Free Online Library. If you've got the AN/PSN- 1. GPS receiver (DAGR), make sure it's programmed with the right software for safety. Ecm reprogramming software. New Operating Software has been released for field reprogramming of all Army DAGR receivers. Keep your software up-to. Enter the website and download the current software and upgrade your DAGR. Remember, reprogramming erases user and satellite data so.
Coating Description The CLASSIC hard anodizing process is the ideal solution for any application requiring high abrasion resistance and improved corrosion resistance compared to Type II anodizing. Unsealed hard anodize features high bond strength with polymeric coatings and adhesives. CLASSIC aluminum hard anodizing process uses only DC voltage.
Typically coating build is 2 mils / 50 μm that can be sealed or unsealed. The CLASSSIC Hard Coat Process is less prone to burning compared to conventional Hard Anodizing, which also used only DC voltage, due to the addition of SANFRAN in the sulfuric acid electrolyte. Can CLASSIC Aluminum Hard Coat Be Colored? High voltage hard coat oxides darken due to an excess of aluminum atoms in the film, lower porosity compared to Low Voltage Hard Coat, and less uniform cell structures. Also, the low temperature of electrolyte entraps alloying elements back into the oxide causing the oxide to shade: 2000 series – green and gray tones, 5000-dark gray, 6000-almost black, 7000-blue-gray, 8000-high temperature alloy, can be light gray color.
Stephen J Spadafora
Typically, coloring is for identification of the part only – dark burgundy, dark blue, and/or Black are all possible for conventional high voltage coatings at 2 Mils. What Seals Can Be Used for hard anodized aluminum? Both hydrothermal (steam, hot water, Nickel Acetate, Magnesium Acetate, etc.) and precipitating seals (nickel fluoride, di-chromates, etc.) How To Get Maximum Adhesion for Aluminum Hard Coat Unsealed coatings and di-chromate sealed coatings provide the best adhesion characteristics. How to Get Easy Release for Aluminum Hard Coat?
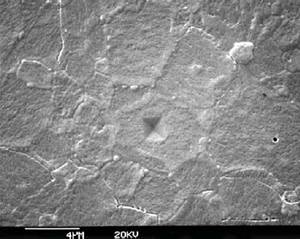
Hydrothermal sealed anodic coatings will have better release characteristics than unsealed or precipitated seal coatings. For enhanced release, specify HARDLUBE PTFE.
What Is the Coating Thickness for Aluminum Hard Coat? Depends on the customer’s requirements. Mil-A-8625 requires 2 mils or 50 μm. Note that the coating both penetrates the surface and builds from the surface in roughly 50% proportions. What Is the Penetration vs.
Build Up for Aluminum Hard Coat? Half of the coating is penetration. Half is Build Up. What Are the Applicable Coating Thickness Tolerances for Aluminum Hard Coat? While an engineered solution can provide tighter tolerances, the general rule of thumb is + / – 20% coating thickness or 0.4 mils on a.002” coating. How Are Parts Racked for Aluminum Hard Coat?
High voltage rectification normally requires 30 Amps per square foot current density. This in turn requires a rack that can hold the current density, and hold the part securely to prevent arching. Typically conventional hard coat will result in a more visible rack mark than rack marks after Type II anodizing, where half the current density is used.
What is the maximum coating thickness for Aluminum High Voltage Hard Coat? Typically for Conventional and CLASSIC Hard Coat, the increasing electrical resistance of the oxide as it builds, coupled with the polarization of the cathode and anode, and the dissolution of the coating left in the electrolyte over time, restricts the formation of a coating much beyond 3 mils. Can Aluminum Cast Materials be Hard Coated? Only aluminum can be converted into aluminum oxide, and silicon in the cast is an impurity. Some cast materials low in silicon can receive a hard coat after selective elimination of surface impurities. However, the higher the silicon content, the less likely a good quality hard coat will ensue. Can aluminum parts receiving the CLASSIC Hard Coat process receive a high gloss or highly matte finish?
Primary factors resulting in a high gloss or high matt finish for a hard coat are not directly related to the aluminum hard coat process. The mechanical finish (mechanical polishing or mechanical bead sanding / blasting) determines macro smoothness or roughness of the substrate. The hard coat anodizing process has secondary factors such as chemical polishing steps and or surface etching. The only factor directly related to the hard coat anodizing process is coating thickness where imperfections in the substrate are “grown” and are thus dependent on coating thickness. To specify gloss and/or matt finish, please conduct an engineering review prior to parts being run. Is Aluminum Hard Anodizing a Plating technique?

Carcinogen
The coating is formed through penetration and build up. A plated coating of 2 mils will add 4 mills to the diameter of a rod where as a hard coat anodizing of the same coating thickness will add 2 mils. What are Edge Defects? The aluminum oxide coating grows perpendicular to the surface. At a sharp edge, there is a gap in the coating. This gap becomes more pronounced as the anodic coating thickness increases.
To eliminate the edge defect, corners should be radiused. Can threads be hard anodized?
Note the pitch diameter decreases by 4 times the coating thickness on internal threads and increases 4 times on external threads. Do final tolerances need to allow for hard anodizing? Yes – the final specification needs to allow for 1/ 2 the coating thickness.
Comments are closed.